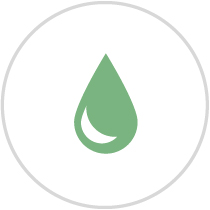
Laboratory Recordkeeping for Supervisors
Course Description:
Welcome to the training session on laboratory recordkeeping for supervisors. We’ll cover all the basic laboratory safety records you have to maintain concerning the use of hazardous chemicals in the lab. We’ll talk about how to comply with federal Occupational Safety and Health Administration, or OSHA, rules for recording workplace injuries and illnesses; maintaining safety data sheets, or SDSs, and chemical inventories; maintaining employee exposure and monitoring records related to occupational chemical exposures; and certifying that you have provided personal protective equipment training, or PPE, training, to employees who use PPE. You’ll want to have all these records on hand if an OSHA inspector visits your facility. We’ll also cover some laboratory recordkeeping guidelines that, though not required by law, will help you document compliance with other OSHA rules related to laboratory safety.
Why “Laboratory Recordkeeping for Supervisors” Matters:
Before we talk about the recordkeeping requirements in detail, we’ll outline the types of records that we’ll cover in this training session.
The written CHP, though it’s not officially called a ”record,” must be maintained at the workplace.
The most common types of records are what’s known as the OSHA 300 forms, or injury and illness records, for a facility where there are 11 or more workers at any time during the calendar year.
You must keep records of any employee exposure to a hazardous chemical, chemical exposure monitoring reports, and related medical consultations or evaluations.
You must keep SDSs for all hazardous chemicals used or stored at the facility or an inventory of chemicals used at the facility if SDSs for chemicals no longer used are not available.
Where employees wear PPE such as respirators, you must keep a number of records, including written certification that employees required to wear PPE have been trained how and when to use it.
Also, there are other important records that should be kept, though not required by regulation, including records of facility inspections, safe work practices, employee training, and inventories of usage of high-risk chemical substances.
Key Points:
You must keep the following records if you are classified as a general industry facility with more than 10 employees, you have hazardous chemicals or other harmful physical agents, and if any of your employees use PPE:
- CHP,
- OSHA 300 injury and illness records,
- SDSs or chemical list,
- Medical and exposure monitoring records,
- PPE training certification, and
- Respiratory protection medical evaluation and fit test records.